
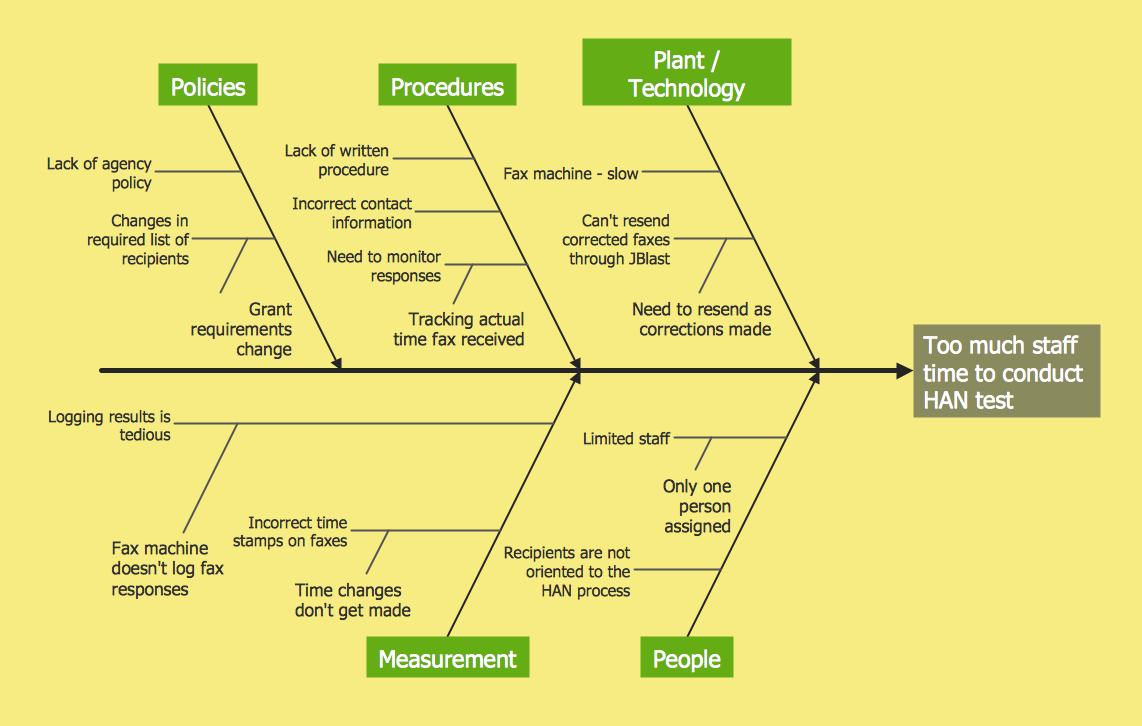
These should be broad categories to guide brainstorming, such as Equipment, Environment, Rules/Procedures, and Staff/People. Second, consider what types of factors could have contributed to the problem. Step 2: Identify the Potential Factors Causing the Problem A patient was given a dose of a medicine they reported being allergic to, causing them to experience a medical emergency.An uncredentialed person accessed the production facility, contaminating several batches of our product.Quality check has found three times more faulty products in the past two months compared to the previous period.This problem statement goes at the “head” of the fish. Identify and agree upon a clear problem statement that aligns everyone around the failure or issue they need to address. Once you have representation from multiple roles or impacted areas of your business, you can brief everyone on the challenge and get started. The first step to brainstorming causes with an Ishikawa diagram is pulling together a cross-functional team to address the failure or problem with multiple areas of expertise. Step 1: Assemble Your Team and Identify the Problem RCA is often used to understand system failures or near-misses. The American Society for Quality defines root cause analysis (RCA) as “the method of uncovering the accurate reason(s) why something is happening or has already occurred.” RCA uses several techniques to identify causes and is part of the field of total quality management.
#Simple fishbone diagram example how to
Get started with a free trial of Gliffy to make your own fishbone diagram > How to Use an Ishikawa Diagram for Root Cause Analysis What is Root Cause Analysis? Manufacturers need to ensure that their output is consistent and predictable, so understanding what could cause variation will help them create better processes. By considering what can go wrong, designers can strengthen each step or adjust the process to be as efficient and reliable as possible.īecause fishbone diagrams work by identifying possible issues and failures, they’re especially valuable in fields like supply chain management and manufacturing. Brainstorming everything that could cause a process to fail helps process owners manage existing processes, but can be even more effective while designing a new process. TRY GLIFFY What is a Fishbone Diagram Used For?įishbone diagrams work by helping process designers brainstorm the potential causes for a particular problem. Want to get started right away? Make an Ishikawa diagram with a free trial of Gliffy: How to Use an Ishikawa Diagram for Root Cause Analysis.To learn more about fishbone diagrams, read on or jump ahead to one of the following sections: Kaoru Ishikawa created the fishbone diagram structure, so you’ll also see them referred to as Ishikawa diagrams or cause and effect diagrams. A fishbone diagram is a way to visually represent the potential causes of an event or problem.
